Merry Christmas and Happy New 2023
It’s the most wonderful time of the year and our customers are the most wonderful part of our business! The team at EccoFab wishes you all a joyous Christmas and a prosperous New Year.
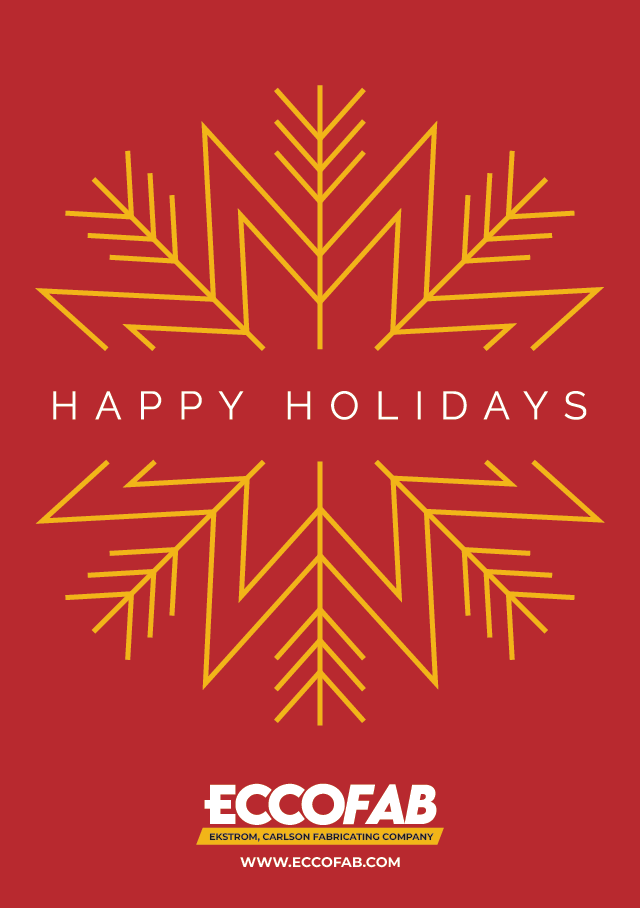
It’s the most wonderful time of the year and our customers are the most wonderful part of our business! The team at EccoFab wishes you all a joyous Christmas and a prosperous New Year.
We are excited to announce that our company will be showcasing our latest wear parts for the aggregate industry at the upcoming CONEXPO-CON/AGG trade show in Las Vegas, Nevada! We will be located at Central Hall – Booth #30958. We invite you to come see us and learn more about…
SSAB, the company behind Hardox® steel is taking the lead in reducing the carbon footprint of the steel industry and is aiming to launch the world’s first fossil-free steel by around 2026. SSAB has produced the world’s first fossil-free steel and delivered it to a customer. The trial delivery is…
At EccoFab, we’re constantly pushing the boundaries of design, engineering, and innovation to create wearparts that not only withstand the toughest conditions but also simplify operations for users. We’re excited to present Generation 2 of our groundbreaking single hole, quick-release wedges. This innovative product is the result of our unwavering…
EccoFab’s Heat Resistant Asphalt Drum Flighting Makes “Asphalt Contractor’s Top 30 Products 2024 We are thrilled to announce that EccoFab’s Heat Resistant Asphalt Drum Flight has been named one of Asphalt Contractor’s Top 30 Products for 2024. This prestigious list recognizes the best new products and long-standing innovations in the…
Our client, operating in an exceptionally demanding work environment, faced a recurring and challenging issue. Their OEM cutting edges, typically designed to last for extended periods, were lasting a mere 10 weeks in this rigorous setting. This rapid wear rate presented a double-edged problem. Firstly, it significantly escalated their maintenance…
For over four decades, Gerry has been a pioneer in the aggregate industry, working closely with SSAB and leveraging the power of Hardox® steel to produce top-quality wearparts. These prestigious recognitions are testaments to his unwavering dedication, expertise, and the exceptional products EccoFab has delivered to clients throughout the years….